Virtual Commissioning Success Story
Virtual Commissioning for Assembly Line
Automaker, Germany
Project Overview
We partnered with an automaker to implement Virtual Commissioning for their Transmission Middle Housing Machining Line. The project aimed to optimize material flow, develop efficient strategies, and reduce commissioning costs and time. Leveraging industry-leading software such as Siemens Process Simulate, Kuka Office Lite, Siemens S7 Simatic Manager, WinMOD, and SIMIT, our team successfully delivered exceptional results.
Requirements
The project encompassed the following key requirements:
Development of a virtual factory for the Transmission Middle Housing Machining Line.
Logic development for the complete material flow, including various strategies such as automatic conveyor lane sorting for 73 different part types, identification systems, and testing equipment.
Emergency strategy development and implementation, including error handling for situations such as washing machine errors, error correction in the Machining Centre, robot bypass, manual inspection in case of scanner error, master part measurement, and rework and reject part strategies.
Achievements
By collaborating closely with the automaker, our team successfully achieved the following outcomes:
- Early Error Detection: Through extensive testing and simulations, we identified and rectified potential errors six months before the start of production (SOP). This early detection allowed for proactive measures and ensured a smooth commissioning process.
- Cost and Time Savings: The implementation of Virtual Commissioning significantly reduced commissioning costs and time. By optimizing material flow, developing efficient strategies, and addressing potential issues beforehand, the automaker experienced substantial savings in terms of resources and project timelines.
- Enhanced Efficiency and Reliability: The virtual commissioning process enabled the automaker to fine-tune the material flow and strategies, leading to improved efficiency and reliability in the assembly line. The automatic conveyor lane sorting for different part types and the implementation of emergency strategies ensured smooth operations and minimized production disruptions.
Customer Satisfaction
Our expertise in Virtual Commissioning, coupled with the successful implementation of the project, resulted in high customer satisfaction. The automaker witnessed the tangible benefits of our solutions, including early error detection, cost and time savings, and enhanced efficiency. The collaborative partnership between our teams ensured a seamless project execution and a successful outcome.
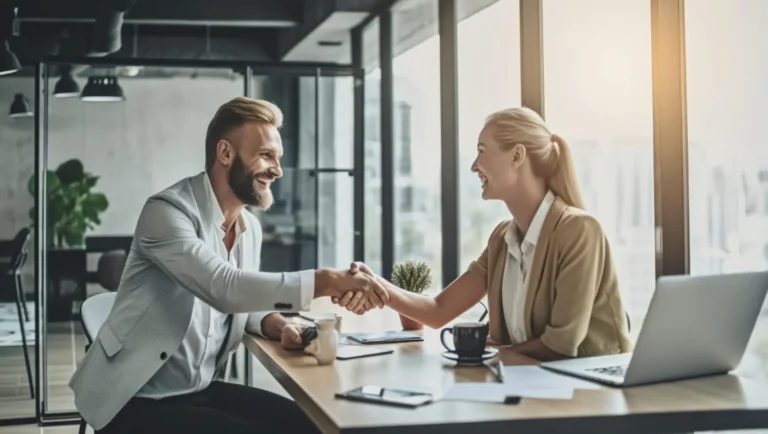
Conclusion
The Virtual Commissioning project for the Assembly Line of our automaker client exemplifies our commitment to delivering innovative solutions and driving operational excellence. By leveraging advanced software technologies and our expertise in logic development and strategy implementation, we achieved remarkable results. Contact us to learn more about how our Virtual Commissioning services can optimize your manufacturing processes and accelerate your time-to-market.